A MILLION MILE RIDE WITH OUR FRIEND THE THRASHER? TRUST US, IT HURTS. THANKFULLY, IT'S SIMPLY HOW WE MAKE SURE YOUR RIDE DOESN'T.
There are many wheels available today - some are a collection of miscellaneous parts chosen for price or color. Some are true systems. To build a wheel that provides best in class aerodynamics, stiffness, durability and great handling can’t be done with just parts out of a catalog. This system needs to be engineered and then it needs to be tested. A lot. At Rolf Prima, we pride ourselves on our engineering but we don’t pat ourselves on the back until we’ve validated it through testing. We’ve developed a testing regime that puts our wheels through the ringer, be it impact, braking, durability – you name it! Below is a sample of some of our proprietary tests.

IN-HOUSE DRUM TESTER: MEET "THRASHER"
Field testing is part of our program, but wheels need to be driven harder in lab testing to make sure they are ready for all forms of use. That's why we developed our in-house drum fatigue tester that allows us to put the hard miles the wheels need in a matter of days vs. years. Read more about our Fatigue Tester.

STOPPING IS REALLY IMPORTANT
While it has been said jokingly many times that brakes just slow you down, that is a really good thing. Having brakes that do exactly what you expect them to do when you expect them to do it, is not as straightforward as it seems. That's why at Rolf Prima, we’ve developed testing capabilities specifically to evaluate the energies resulting from braking forces, distances and temperatures to ensure that brake performance is not something you need to think about. Read more about our Brake Testing.

PERFORMANCE: AERODYNAMICS AND HANDLING
While a lot of our testing is strength and durability focused, we spend equal time in performance testing. How a wheel rides is important if seemingly somewhat harder to quantify. Testing a wheel in a wind tunnel shows how a wheel responds to wind at different angles with or without a rider giving insight into overall aerodynamic efficiency as well as crosswind handling. Our professional athletes pile on the miles on new wheel designs to confirm our lab tests. Read more about our Aerodynamics.

IMPACT
Our impact test is designed to simulate the extremes of riding in the real world, using a weight calibrated steel anvil to impact the wheel. We test to the UCI standard (40J), then go on to test at even higher levels using our in-house standard. Using adjustable height and weight, we can develop different impact energies to evaluate the impact resistance of the wheel at different points. We then measure at spokes, in between spokes and at the valve hole to ensure all parts of the wheel meets expectation. See our Impact test in action.
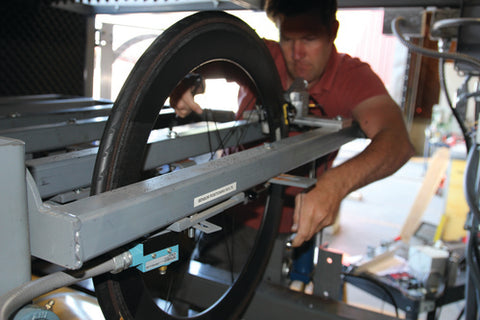
STIFFNESS
A term that is thrown around a lot with wheels, stiffness plays into wheel performance in a lot of different ways. How a wheel goes into and snaps out of corners, how it responds in powering up a hill and how comfortable it is to ride are attributes that can be tuned – if you test them. As a team that rides and races just about every cycling discipline, we know what we want a wheel to feel like and by testing the wheels, we can tune their design to match.
There are multiple aspects to stiffness and to best simulate the real world, we test them in isolation and combination. We test the lateral and radial stiffness of rims to get a picture of the expected performance and ride characteristics before we build them into a wheel. Tensioned spokes behave differently depending on loading and in real life the lateral and radial loads occur in combination. This means stiffness needs to be tested in more complicated ways to understand how the wheel will react. This is not straightforward (or linear) but it is important to the overall performance of our wheels.
In a perfect world of smooth pavement, any wheel build could work. However, in the real world of poor roads, potholes, surprise rocks and curbs, the resilience of a wheel is important.
LATERAL STIFFNESS TESTER
When we’re developing a wheel, we perform numerous tests to get information about different aspects of the wheel – and lateral stiffness is one of them. Lateral stiffness comes into play because it affects how a wheel rides. Having good lateral stiffness can mean the difference between whether a wheel feels snappy or a wheel feels spongy. It is not the whole story, but it is an important piece of it.
Our stiffness tester allows us to measure a wheel’s stiffness in a continuous way, so we can see how the wheel behaves under a lateral load as the geometry of the wheel changes with deflection. With this test fixture, we can slowly apply lateral force to a rim and measure how much load it takes to deflect the wheels over lateral distance.
The stiffness test begins by measuring the initial location of the rim on the fixture then applying a small preload to eliminate any slack in the system. We gradually apply a lateral force working up to our maximum load. Once reached, we hold that load on the rim for 60 seconds. The load is then released and the rim’s location is measured again, comparing it to the initial measurement. We also check trueness. We also use the same fixture for lateral strength testing. This is an overload test where we measure how much lateral force a wheel can absorb. In getting these precise measurements, we can see how each change in specification changes a wheel’s stiffness and it is with this is the iterative process that we use to really dial in the ride feel and quality of a wheel.